News
News Company
The Automatic DebugRobot software is worth gold for EMS providers
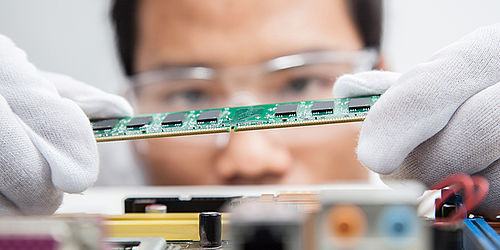
The Automatic DebugRobot was originally developed at the request of an EMS service provider, Surface Art Engineering, which operates as a central point of contact for simplifying the process of launching products to the market.
The San José, California-based, women-owned company, founded in 1994, offers a full range of Printed Circuit Board Assembly (PCA) and mechanical assembly for prototype, pilot production and volume production to a broad range of companies and industries. Its customers include start-up companies that develop and introduce new products, as well as established companies that require the collaboration, quality, and service of a contract manufacturer.
Since 2013, Surface Art Engineering is successfully using our Condor Flying Prober to test their customer boards. In addition, they use our Automatic Program Generator (APG) from CITE to automatically generate programs and C-LINK to generate fixture data.
Surface Art Engineering believes that product velocity is the key to meeting a market window and because they strive to always meet their customers' expectations, they want to help their clients to expedite their time-to-market of their products even faster. One of the lengthiest processes of orders fulfillment was often the debugging times, especially for larger boards with more than 500 nets, it took the engineers a lot of time and programming effort.
So, Surface Art Engineering asked us if we could develop a process that could automatically debug test programs, for them fulfill their orders faster and for their clients to be able launch their products faster to the market. We found the idea exciting and accepted the challenge. We set ourselves the goal of creating a process that automatically debugs to minimize the programming effort. The idea was to save the programmer valuable time and cover more measurement types, to add functions that have the greatest effect to save the most time for the programmer.
This is how the DebugRobot was created. Surface Art Engineering was the first customer of our DebugRobot and can automatically debug up to 80 % of the device under test and the programmer only must check a few measurements manually. With the help of the DebugRobot they were able to reduce their debugging time enormously. For example, a board with 1.000 nets, an engineer previously needed 2 weeks to debug one board, now by using the DebugRobot, an engineer can debug 6 boards in 2 weeks. It not only saves the engineers valuable time, but also it automatically selects the best guarding points, stabilizes measurements i.e. to achieve the lowest possible standard deviation of the values when repeating measurements. Usually, for transistor tests the pin order needs to be determined manually and errors can easily occur here. Now, with the DebugRobot the pin order is automatically detected and can even be corrected because it has a built-in intelligence. Not so with the DebugRobot, the DebugRobot can correct the mixed pin sequence itself without having to intervene manually. It can also automatically learn all the measurements of the diodes tests without any user intervention.
Surface Art Engineering has saved the engineers valuable working time with the DebugRobot, even checked some tests qualitatively and helped to process more orders faster and significantly reduced the time to market for their customers.
The DebugRobot saves valuable time and even helps to correct manual test program preparation errors, which are two factors that are especially essential for EMS service providers. Today the DebugRobot is an extension of the CITE 8 software. The more networks a board has, the more time is saved when debugging.
Find out more about the DebugRobot and the CITE 8 software here